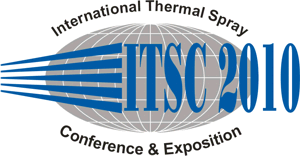 |
Abstract No.: |
|
Title: |
The oxy fuel ionization (OFI) process: experimental process analysis
|
|
Authors: |
Maria Parco / INASMET-TECNALIA , Spain Georgiy Barykin / Inasmet Tecnalia, Spain Ignacio Fagoaga/ Inasmet Tecnalia, Spain Gilles Mariaux/ SPCTS, University of Limoges, France S. Goutier/ SPCTS, University of Limoges, France Michel Vardelle/ SPCTS, University of Limoges, France
|
|
Abstract: |
The Oxy-Fuel Ionization (OFI) is a new thermal spray process which has been under development at the Inasmet facilities. The OFI system consists basically on a high velocity combustion process which is assisted by the incorporation of a low energy plasma source before the combustion chamber. The continuous addition of ionized and heated gas species to the combustion mixture allows using over a large range of fuel/oxidant conditions, lower gas flow rates and higher powder feed rates than conventional HVOF guns. The OFI gun has been designed following a highly modular concept, which in combination with the high flexibility of the system in terms of fuel/oxidant consumption, is expected to allow the deposition of coating materials with the most different physical and chemical natures, but with superior properties than those achieved by other even versatile spray processes working in the low velocities range. This work deals with the experimental analysis of the process and its correlation with the deposition of carbide based powder materials. Two in-flight particle diagnostic systems were implemented: -the Spray Watch diagnostic system (from OSEIR), to study the influence of the gun nozzle design on the particle velocity and temperature, -the Spray and Deposit Control (SDC) system (developed by the SPCTS laboratory of the University of Limoges), to optimize the hot particle spray jet and achieve the highest efficiency from the process. Coating properties (micro hardness distributions on the coating cross section and crystallographic structures) correlated to particle measured parameters allow a better understanding and thus control of the process.
|
|