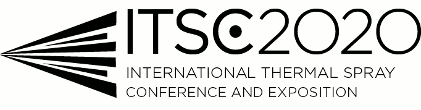 |
Abstract No.: |
|
Scheduled at:
|
Thursday, June 11, 2020, Hall G2 3:00 PM Aviation Industry III
|
|
Title: |
An Al6061/NiTi composite by cold spray and friction-assisted processing: deposition mechanism and properties
|
|
Authors: |
Chunjie Huang* / Northwestern Polytechnical Univerisity, China Alexander List / Helmut Schmidt University, Germany Frank Gärtner/ Helmut Schmidt University, Germany Benjamin Klusemann/ Helmholtz-Zentrum Geesthacht, Germany Thomas Klassen/ Helmut Schmidt University, Germany
|
|
Abstract: |
Bulk nickel titanium or nickel titanium-composite parts are employed in damping applications. However, due to the reactivity and the super-elastic behavior of NiTi, possible process routes for casting, sintering, as well as shaping and machining are difficult to apply and quite costly. Thus, new techniques for additive manufacturing of respective parts are needed for paving the way to widespread applications. Using NiTi-Al6061 composites as model system, the present study suggests a new process route by combining cold spraying and friction stir processing for building up layers or parts. Al-alloys can be processed to dense coatings by cold spraying. In contrast, super-elastic NiTi can in maximum be build up as monolayer. Thus, due to the difference in mechanical strength and the thermal softening behavior, bonding during cold spraying of respective blends is solely caused by the deformation of the Al-alloy powder particles, the strength of internal interfaces between the two constituents being far below optimum. Friction stir processing is applied to reduce the amount of microstructural defects as porosity and non-bonded internal interfaces, and thus improving the mechanical performance of cold sprayed parts. The composites manufactured by using cold spraying followed by friction stir processing have a homogenous NiTi distribution and well bonded NiTi/Al6061 interfaces. By individual parameter optimization, the formation of undesired intermetallic phases can be avoided. The results on microstructures and strengths of as deposited and additionally friction stir processed composites are discussed with respect to the deposition mechanism and the microstructural evolution during post-processing, as well as needed interface qualities to serve as damping material.
|
|