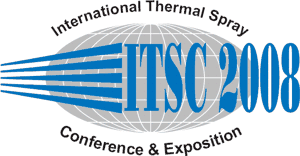 |
Abstract No.: |
|
Title: |
Microstructure and wear resistance of plasma sprayed carbides and ceramic coatings deposited on an Invar® alloy surface
|
|
Authors: |
Carlo Giolli* / Turbocoating SpA, Italy Michele Turbil / Politecnico di Torino, Corso Duca degli Abruzzi, 24 - 10129 , Italy Mario Rosso/ Politecnico di Torino, Corso Duca degli Abruzzi, 24 - 10129 , Italy Gabriele Rizzi/ Turbocoating S.p.A., Via Mistrali 7, Rubbiano di Solignano, Italy Andrea Scrivani/ Turbocoating S.p.A., Via Mistrali 7, Rubbiano di Solignano, Italy
|
|
Abstract: |
Microstructure and wear resistance of plasma-sprayed carbides and ceramic coatings deposited on an Invar® alloy surface.
M. Turbila, C. Giollib, G. Rizzib, M. Rossoa and A. Scrivanib
aPolitecnico di Torino, Corso Duca degli Abruzzi, 24 - 10129 Torino, ITALY bTurbocoating S.p.A., Via Mistrali 7, Rubbiano di Solignano, Parma, Italy
Abstract Invar® alloy (Fe ? 36%Ni) is widely used in industrial applications which require high dimensional stability because of its exceptionally low thermal expansion coefficient, while thermal spray techniques are frequently used for improve wear and corrosion resistance of the substrate material and/or protect it from the higher temperatures of the surrounding environment. Purpose of this work is to study a surface treatment of Invar® alloy in order to enhance the performance of molds for the production of carbon fiber reinforced plastic (CFRP) components. Four different kinds of commercial powders were sprayed on an Invar® substrate: aluminium oxide (alumina) mixed with titanium oxide (titania), chromium oxide and yttria partially stabilized zirconia (YSZ) by Air Plasma Spray (APS), and tungsten carbide in cobalt-chromium metallic matrix based by High Velocity Oxygen Fuel (HVOF). An investigation of microstructure has been carried out by means of metallographic microscopy observation and SEM analysis, and microhardness profile evaluation by means of Vickers indentation testing. Finally, friction behaviour and wear resistance were evaluated and compared in dry sliding conditions with Pin-On-Disk apparatus (according to the standard ASTM G 99) for not coated Invar® substrate and for the different coated substrates.
|
|