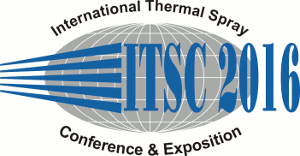 |
Abstract No.: |
|
Title: |
Atmospheric plasma spray manufacturing of TiO2-x metal oxide gas sensors onto ceramic substrates for high temperature applications
|
|
Authors: |
Sergi Dosta* / Thermal Spray Centre (CPT) - Universitat de Barcelona, SPAIN M. Robotti / Thermal Spray Centre (CPT) - Universitat de Barcelona, Spain O. Monereo/ Department of Electronics (MIND) - Universitat de Barcelona, Spain IG. Cano/ Thermal Spray Centre (CPT) - Universitat de Barcelona, Spain A. Cirera/ Department of Electronics (MIND) - Universitat de Barcelona, Spain JM. Guilemany/ Thermal Spray Centre (CPT) - Universitat de Barcelona, Spain
|
|
Abstract: |
Nowadays contamination in urban atmospheres is increasing and more pollutants control in the environment is needed. Metal oxide (MOX) gas sensors coatings can help detecting quantities of hazardous particles in gas phase. The development of a TiO2-x active layer by Atmospheric Plasma Spray in a gas sensor consisting of thin ceramic substrate was the target of this research. The principle of operation of MOX devices is the change of the electrical resistance depending on the gas surrounding due to the chemical reactions that are developed onto the metal oxide surface. The performance depends on three key-steps: i) receptor function, which determines the adsorption of the gas on the metal oxide surface, ii) transducer function, which is in command to transform the chemical interaction towards an output signal and iii) approachability, that eases the access of the gas into the inner grains of the solid. Thermal Spray (TS) techniques and in particular Atmospheric Plasma Spray (APS) represent rapid manufacturing systems for depositing the active layer in a MOX sensor with the aim of solving the desired requirements. APS spraying conditions have been adjusted in order to achieve well-bonded and active coatings onto thin ceramic substrates having on the top printed electrical circuits. The hydrogen present in the plasma reduces the MOX powder and this way influences the activity of the final coatings. Performances of the devices have been tested using CO, NO2, NH3 and ethanol in gas phase at different temperatures and concentrations. These results represent an innovative trend for a new generation of ceramic gas sensors which can be used at high temperatures and can detect various gases concentrations.
|
|