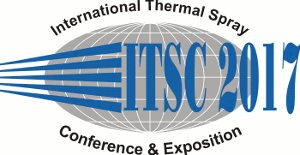 |
Abstract No.: |
|
Scheduled at:
|
Thursday, June 08, 2017, Hall 12 11:40 AM Aviation & Power Generation Industry II
|
|
Title: |
Mechanical properties of YTTRIA-stabilised-zirconia for thermal barrier coating Systems: Effects of testing procedure and thermal aging
|
|
Authors: |
Pierre Planques* / CIRIMAT - Safran Helicopter Engines, France Vanessa Vidal/ Mines Albi, ICA (Institut Clément Ader), FRANCE Philippe Lours/ Mines Albi, ICA (Institut Clément Ader), FRANCE Vincent Proton/ SAFRAN HELICOPTER ENGINES, FRANCE Fabrice Carbos/ SAFRAN HELICOPTER ENGINES, FRANCE Julitte Huez/ CIRIMAT, France Bernard Viguier/ CIRIMAT, FRANCE
|
|
Abstract: |
Cyclic oxidation failure of Atmospheric Plasma Sprayed Thermal Barrier Coatings (APS TBCs), commonly used to insulate hot sections in gas turbines, usually results from the spallation of the ceramic top coat. Consequently, in order to predict such spalling phenomena, understanding the mechanisms for cracks initiation and propagation in thermal barriers is of utmost concern for engine-makers. Microstructures of the coatings is known to play a major role in the failure. This work summarizes the main outcomes of a comparison between two microstructures of TBCs i.e. standard lamellar, porous and micro-cracked microstructure, and Dense Vertically Cracked (DVC) microstructure. Lifetime assessment, effect of cycle duration and crack propagation during high temperature thermal fatigue testing, were investigated for both standard and DVC microstructures. In this purpose, a dedicated instrumented cyclic oxidation rig allowing to establish thermal gradient through the thickness of TBCs was used to impose critical conditions as close as possible to in-service environment. Specimen surface temperature is set at 1150°C and back temperature of the underlying substrate is about 800°C. The number of cracks, the crack length as well as the crack opening distance have been monitored for different pre ageing treatments. A comparison with results reported in the literature is also proposed. The mechanical behaviour of the TBCs is obtained by three points bending tests and Small Punch Tests (SPT). Specifically, a modified non-standard SPT device, that can be used up to 1000°C in a natural air environment has been developed. Both standard and DVC APS TBCs specimens are tested, following various isothermal heat treatments at 1100 °C and 1200 °C. The evaluation of the tensile mechanical properties, strength and fracture toughness derived from those test methods is based on finite element calculations, willing to build and properly implement a relevant model for TBC life suitable and appropriate for design purpose.
|
|