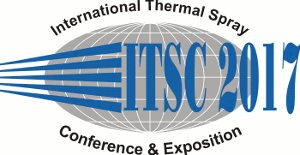 |
Abstract No.: |
|
Scheduled at:
|
Thursday, June 08, 2017, Hall 28 9:20 AM Modeling & Simulation I
|
|
Title: |
A comparative CFD study of the influence of combustion chamber geometry in the HVSFS process
|
|
Authors: |
Martin Plachetta* / University of Stuttgart, Germany Patrick Eckert / Institute for Manufacturing Technologies of Ceramic Components and Composites (IFKB), University of Stuttgart, Germany Peter Krieg/ Institute for Manufacturing Technologies of Ceramic Components and Composites (IFKB), University of Stuttgart, Germany Andreas Killinger/ Institute for Manufacturing Technologies of Ceramic Components and Composites (IFKB), University of Stuttgart, Germany
|
|
Abstract: |
Suspensions have shown a great potential for being employed as the spraying materials in flame spraying processes with the aim of producing thin and dense coatings. The internal axial injection of a suspension within processes like the high-velocity suspension flame spraying (HVSFS) offers the advantage of complete suspension entrainment within the gas stream, which therefore results in enhanced momentum and heat transfer to the particles. Experimental assessment of the achieved particle velocities and temperatures within the combustion chamber is nonetheless practically infeasible. A better insight into the process is attainable through employing computational simulations. Following a computational fluid dynamic (CFD) modelling approach for HVOF processes, combustion and gas flow turbulences were simulated for different combustion chamber geometries and ethene/oxygen ratios commonly used in the HVSFS process. Simulations were done in ANSYS CFX. To account for the highly turbulent flow characteristics, the SST-model was chosen, employing a global two step reaction eddy-dissipation-model for fuel gas combustion. Second-order high resolution discretion was used to enable a good resolution of flow features like shock diamonds. The results of the simulation were compared to experiments employing the modelled combustion chambers and gas ratios. Parameters like chamber pressure, cooling water temperature and heat flux of the flame were monitored in order to allow a qualitative evaluation of the calculated values.
|
|