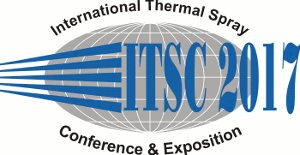 |
Abstract No.: |
|
Scheduled at:
|
Thursday, June 08, 2017, Hall 28 4:00 PM Cold Gas Spraying II
|
|
Title: |
Impact Energy as a unifying concept for comparison of kinetic and thermal spraying
|
|
Authors: |
Hamid Assadi / Brunel University London,
Brunel Centre for Advanced Solidification Technology (BCAST), United Kingdom Sebastian Krebs / Helmut-Schmidt-University, Institute of Materials Technology, Germany Makoto Watanabe / National Institute for Materials Science, High Temperature Materials Unit, Japan Seiji Kuroda/ National Institute for Materials Science, High Temperature Materials Unit, Japan Hiroshi Katanoda/ Kagoshima University, Department of Mechanical Engineering , Japan Werner Krömmer/ Linde AG, Linde Gases Division, Germany Frank Gärtner*/ Helmut-Schmidt-University of the Federal Armed Forces, Germany Thomas Klassen/ Helmut-Schmidt-University of the Federal Armed Forces, Germany
|
|
Abstract: |
For cold spraying, coating properties have been shown to correlate with the ratio of particle impact velocity to the critical velocity, also referred to as the coating quality parameter eta. This concept has limits for high temperatures. Considering thermal softening, the critical velocities for bonding become rather small at high temperatures and vanish at the melting point of a material. Thus, finite impact velocities at high impact temperatures result in very high eta values. For particle temperatures above the melting temperature, as in thermal spraying, this description fails completely. Therefore, the use of total particle energy is suggested for the description of particle or droplet bonding and the attainable coating properties, as a unifying concept for both kinetic and thermal spraying.
To explore this new concept, cold spraying, warm spraying and HVOF-spraying were applied over a wide parameter range for the example of nickel-aluminium bronze as feedstock. Particle / droplet impact conditions were calculated by computational fluid dynamics. As a measure of the extent of bonded internal interfaces, the coating tensile strength, the electrical conductivity as well as coating cavitation resistance were determined. The results show that coating properties correlate well with increased impact energies, although with different slopes for kinetic spraying and thermal spraying. This difference in needed energy input for splat bonding and improved coating properties is interpreted in view of temperature distribution within the particle. In thermal spraying, the whole particle volume is at high temperatures, whereas in kinetic spraying, the deformation causes a local heat rise at the interface only. As compared to thermal spraying, the lower critical energies for bonding in kinetic spraying indicate that heating of the whole particle is not needed for bonding. Thus, kinetic spraying is more energy efficient in this respect, however requires ductile materials for heat generation.
|
|