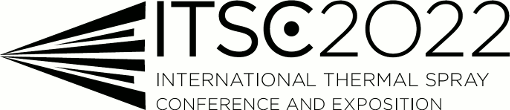 |
Abstract No.: |
|
Scheduled at:
|
Friday, May 06, 2022, Hall G1 9:00 AM Laser Cladding
|
|
Title: |
Thermal monitoring of laser cladding processes with visible, near-infrared, and shortwave infrared camera systems
|
|
Authors: |
Dmytro Havrylov* / Xiris Automation Inc., Canada Gentry Wood / Apollo-Clad Laser Cladding, Canada Patricio F. Mendez/ University of Alberta, Canada
|
|
Abstract: |
Laser cladding is a modern process used to deposit high performance wear and corrosion resistant coatings. With a push in industry for maximum productivity and the increasing trends towards direct energy deposition (DED) additive manufacturing (AM), there is a need to control the process adaptively. Thermal monitoring of the molten clad pool is a promising avenue of process control for these applications. The areas of interests include the melt pool geometry, the deposited clad bead, and the powder flow. Midwave infrared (MWIR) cameras are often used for thermal monitoring in laser cladding. They normally have a low resolution and require a special non-glass optics. SWIR are reported to be able to combine the benefits of MWIR systems and visible light cameras. This work focuses on the experimental comparison of the camera systems working in visible (VIS), near-infrared (NIR), and shortwave infrared (SWIR) applied to laser cladding. The tests were performed with Inconel 625 powder onto the substrates of Inconel 718 and 4140 and 4330V alloy steels and spherical tungsten carbide in Ni-B-Si matrix onto 4330V. The experimental set up included the ytterbium fiber laser with the working wavelength of 1070 nm. In the SWIR band, the thermal emission of the melt pool, the cooling clad bead and the powder was clearly visible. In the VIS and NIR spectra, only the powder flow through the laser beam was detectable. The melt pool width, length and area were imaged with a SWIR camera and then measured using a Blob algorithm. The effect of the variations in the laser power, travel speed, and powder feed rate on the Inconel 625 melt pool was investigated. The melt pool length and area were found more sensitive to the variations in the process parameters than the melt pool width.
|
|