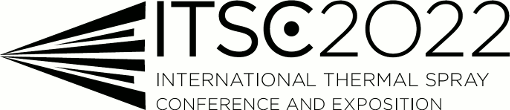 |
Abstract No.: |
|
Scheduled at:
|
Friday, May 06, 2022, Hall G1 12:20 PM Cold Gas Spraying III
|
|
Title: |
Particle acceleration through coaxial Co-flow nozzles for cold spray applications
|
|
Authors: |
Amit Kumar Sharma* / South East Technological University, Ireland Ashish Vashishtha / Department of Aerospace, Mechanical and Electronic Engineering, Institute of Technology Carlow, Ireland Dean Callaghan/ The Center for Research and Enterprise in Engineering (engCORE), Institute of Technology Carlow, Ireland Cathal Nolan/ Department of Aerospace, Mechanical and Electronic Engineering, Institute of Technology Carlow, Ireland Srinivasa Bakshi/ Department of Metallurgical and Material Engineering, Indian Institute of Technology Madras, India M Kamaraj/ Department of Metallurgical and Material Engineering, Indian Institute of Technology Madras, India Ramesh Raghavendra/ SEAM Research Centre, School of Engineering, Waterford Institute of Technology, Ireland
|
|
Abstract: |
Keywords: cold spray, computational fluid dynamics (CFD), co-flow nozzle, gas flow
Abstract:
The cold gas dynamic spray (CGDS) process is an emerging non-thermal deposition method that has gained a lot of attention from scientists and the industrial community due to its vast potential for additive manufacturing applications. In the cold spray process, bonding takes place when the velocity of the particles, which are accelerated by high pressure and pre-heated supersonic gas stream, exceed a critical velocity. While a lot of attention has been given to the deposition of various materials through cold spray, very few studies at present deal with advanced nozzle designs to simultaneously improve the efficiency and build quality of the deposition. The particle acceleration process in the nozzle, as well as its multiphase nature, are key aspects of the cold spray process. Furthermore, the longer divergent section in traditional circular nozzles is subjected to clogging, which in turn leads to shorter continuous run times. In this study, a coaxial co-flow nozzle is introduced with the view to enhancing the deposition efficiency (DE) and reducing the divergent section length by providing a wall of high-speed fluid around primary jet to improve the spatial resolution of the deposited material. CFD simulations and analysis will be conducted on a co-flow nozzle with similar and dissimilar gases where the powder is fed into the central nozzle. Secondary flow in co-flow nozzles [1] has been shown to reduce the growth rate of the primary shear layer and delay the mixing of the primary jet causing the primary supersonic core’s elongation. Furthermore, pressure in the primary and secondary gas flow and nozzle dimensions will be varied and analyzed to understand the effect on both the DE and the particle behavior in the supersonic core.
Reference: [1] Sharma, H., Vashishtha, A., Rathakrishnan, E., & Lovaraju, P. (2008). Experimental study of overexpanded co-flowing jets. The Aeronautical Journal (1968), 112(1135), 537-546. doi:https://doi.org/10.1017/S0001924000002499
|
|