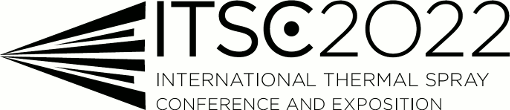 |
Abstract No.: |
|
Scheduled at:
|
Friday, May 06, 2022, Hall D 10:00 AM Additive Manufacturing
|
|
Title: |
In situ measurement and simulation of the shape of a growing cold spray deposit
|
|
Authors: |
Scott Julien* / Northeastern University, United States of America Nathaniel Hanson / Dept. of Electrical & Computer Engineering, Northeastern University, USA Joseph Lynch/ Dept. of Electrical & Computer Engineering, Northeastern University, USA Ozan Ozdemir/ Dept. of Mechanical & Industrial Engineering, Northeastern University, USA Taskin Padir/ Dept. of Electrical & Computer Engineering, Northeastern University, USA Sinan Muftu/ Dept. of Mechanical & Industrial Engineering, Northeastern University, USA
|
|
Abstract: |
Cold spray (cold gas dynamic spray) is a material deposition technology whereby powdered feedstock material is deposited onto a surface at sub-melting temperatures, using a high-velocity stream of gas. The technology is rapidly emerging in a number of industries (military, aerospace, automotive, and medical, among others) for a variety of applications (corrosion-resistant coatings, wear-resistant coatings, dimensional restoration/repair of parts) because of its ability to deposit a wide range of practical engineering materials with relatively high density, low porosity, low number of defects, and good engineering properties. In addition, its high deposition rate and highly controllable spray path make it extremely attractive for creating three-dimensional parts as an additive manufacturing (AM) technology. However, spraying complex shapes requires knowledge of the way in which the deposit shape is built up, and how this is affected by the spray parameters. The present work investigates the process by which deposit shape evolves during spraying. Deposits are sprayed at a variety of AM spray conditions, and the shape buildup process is recorded in real time using an innovative in situ laser profilometry system. The buildup process is examined in detail, including the influence of varying nozzle raster speed and step size, the evolution of deposition efficiency with deposit shape buildup, and evolution of deposit base shape as the deposit grows. The fundamental base shapes measured are used to write custom code to simulate the buildup process, and which is subsequently verified against the experimentally recorded profilometry data. The insights and tools developed through this work provide an advancement in the understanding and prediction of deposit shape. Such work is critical to furthering cold spray’s advancement into the realm of additive manufacturing technologies.
|
|