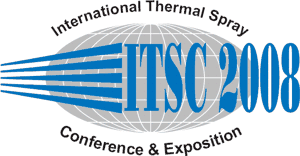 |
Abstract No.: |
|
Scheduled at:
|
Tuesday, June 03, 2008, Room 05 10:10 AM Arc and Laser Spraying Ongoing developments in the field of arc spraying including possibilities for modeling this widely known surface coating technology
|
|
Title: |
Suspension plasma sprayed alumina coating structures: operating parameters vs. coating architecture
|
|
Authors: |
Ghislain Montavon / SPCTS - UMR CNRS 6638, Faculty of Sciences, University of Limoges, France Olivier Tingaud* / SPCTS - UMR CNRS 6638, Faculty of Sciences, University of Limoges, France Alain Grimaud/ SPCTS - UMR CNRS 6638, Faculty of Sciences, University of Limoges, France Alain Denoirjean/ SPCTS - UMR CNRS 6638, Faculty of Sciences, University of Limoges, France Vincent Rat/ SPCTS - UMR CNRS 6638, Faculty of Sciences, University of Limoges, France Jean-François Coudert/ SPCTS - UMR CNRS 6638, Faculty of Sciences, University of Limoges, France Pierre Fauchais/ SPCTS - UMR CNRS 6638, Faculty of Sciences, University of Limoges, France Thierry Chartier/ SPCTS - UMR CNRS 6638, Ecole Nationale Supérieure des Céramiques Industrielles, France
|
|
Abstract: |
Suspension Plasma Spraying (SPS) is a recent technology which permits the manufacturing of thinner (from 5 to 50 µm) layers compared to the ones resulting from conventional plasma spraying. Moreover, SPS is able to process micron-sized and even nano-sized feedstock particles. SPS consists in mechanically injecting within the plasma flow a liquid suspension of particles of average diameter varying between 0.1 and 1 m. Upon penetration within the DC plasma jet, two phenomena occur sequentially: droplet fragmentation and evaporation (lasting, in average, two orders of magnitude longer than fragmentation). Particles are then processed by the plasma flow prior their impact, spreading and solidification upon the substrate. Depending upon the selection of operating parameters, among which plasma power parameters (operating mode, enthalpy, spray distance, etc.), suspension characteristics (particle size distribution, load, viscosity, etc.), and substrate characteristics (topology, temperature, etc.), different coating architectures can be obtained, from dense to porous layers [1]. Nevertheless, the interactions between those parameters which lead to the control of the coating microstructure and its final properties are not yet fully identify. The aim of this study is firstly to understand and determine events occurring upstream during process and secondly to elaborate and quantify functionally graded layers.
[1] P. Fauchais, V. Rat, C. Delbos, J. F. Coudert, T. Chartier, L. Bianchi, Understanding of suspension DC plasma spraying of finely structured coatings for SOFC. IEEE Trans. Plasma Sci. 33 (2) (2005) 920 - 930.
|
|