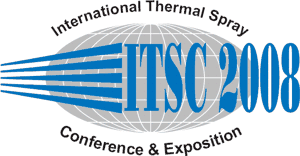 |
Abstract No.: |
|
Scheduled at:
|
Wednesday, June 04, 2008, Room 05 8:20 AM Characterization 1 Modern characterization offers a good possibility for proofing the reliability and the performance of thermal sprayed coatings
|
|
Title: |
Residual stress calculation in thick plasma sprayed coatings
|
|
Authors: |
Hamed Samadi* / Dept. of Materials Science and Engineering, Science and Research Branch, Islamic Azad University, Iran Thomas W. Coyle / Centre for Advanced Coating Technologies, Canada
|
|
Abstract: |
One of the most important parameters controlling the durability of plasma spray coatings is the residual stress, which can be categorized into two components: quenching stress and thermal stress. The quenching stress develops as the solidified splat cools to the temperature of the substrate. Thermal residual stress arises because of thermal expansion coefficient mismatch between the coating and substrate during cooling after deposition. Stresses generated in plasma sprayed coatings can be evaluated by measuring the curvature of the coating on a strip-shaped thin substrate after deposition. Deconvolution of the quenching and thermal components of the stress is difficult. Analysis of multilayer coatings is also problematic. Finite element methods have been used to calculate residual stress levels and the curvature of thin strips. However, many of these models have not considered the build up of stresses during deposition and therefore, the results may not describe the residual stresses of the coating accurately. In this study, a finite element method was employed to calculate thermal stresses during and after deposition of a multilayer coating. The calculations were compared with results from in-situ curvature measurements during deposition on thin substrates.
|
|