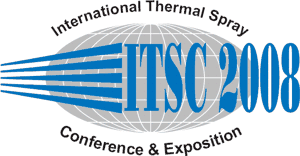 |
Abstract No.: |
|
Scheduled at:
|
Monday, June 02, 2008, Room 04 11:10 AM Wear Protection 1 Special processes for coatings against wear, improved surface roughness of as sprayed coatings, improved sliding behavior
|
|
Title: |
Development of near net-shape coatings for wear and corrosion protection
|
|
Authors: |
Tim Bause* / Leibniz University of Hanover,
Institute of Materials Science, Germany Friedrich-Wilhelm Bach / Leibniz University of Hanover, Institute of Materials Science, Germany Kai Möhwald/ Leibniz University of Hanover, Institute of Materials Science, Germany Martin Erne/ Leibniz University Hannover, Institute of Materials Science, Germany
|
|
Abstract: |
The costs of pre- and after-treatments represent a large part of the total costs in thermal spray processes. Within the production process it is common to apply oversized coatings at first and to grind the coatings to measure afterwards. Thus the applied oversize leads to higher consumption of spray materials and gases during an extended spray process. In addition a significant expense for after-treatments is required. The use of fine narrow fractionated spray materials is seen as a way to reduce operation costs of thermal spray processes. By applying materials with grain sizes below 25 microns thin near net-shape coatings can be realized. These coatings would be conform to requested tolerances in measure and surface properties. With this approach the costs for after-treatments could become redundant or should be decreased significantly at least. In this work several powder materials typically used for wear and corrosion protection (WCCoCr, Cr3C2 NiCr, Cr2O3) were considered for developing near net-shape coatings. In contrast to grain sizes commonly used in thermal spray processes the grain sizes of all investigated powders were specified with maximum 25 microns (-15+5 µm, -20+5 µm, -25+5 µm). In preparation for coating experiments feeding parameters were optimized for several powder feeders. Conventional disc and screw type powder feeders were considered as well as a powder feeder optimized especially for feeding of fine powders. During the coating experiments the HVOF process were used to apply carbide based powder materials (WCCoCr, Cr3C2 NiCr) whereas the APS process was used to apply Cr2O3 coatings. The coatings were examined in terms of deposition efficiency, surface roughness, hardness, fracture toughness, and size accuracy. Furthermore grinding tests were carried out to determine the effort required for after-treatment.
|
|