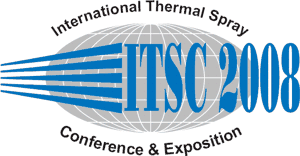 |
Abstract No.: |
|
Scheduled at:
|
Monday, June 02, 2008, Room 04 4:40 PM Printing and Paper - Hard Chrome Replacement Modern coating systems for long lasting printing performance, latest coating developments for rolls in paper machines; Optimized coatings for replacing galvanic hard chrome coatings
|
|
Title: |
Automated substrate cooling system for HVOF coating operations
|
|
Authors: |
Zbigniew Zurecki* / Air Products & Chemicals Inc., USA Ranajit Ghosh / Air Products & Chemicals, Inc., USA Thomas Mebrahtu/ Air Products & Chemicals, Inc., USA Matthew Thayer/ Air Products & Chemicals, Inc., USA Steward Stringer / Air Products & Chemicals, Inc., USA
|
|
Abstract: |
High production rates and feed powder efficiencies are critical in industrial HVOF coating operations such as carbide hardfacing of aircraft landing gear, turbine, and actuator components. A large-scale replacement of carcinogenic, hard chromium plating with WC-Co spray coatings may be successful only with improvements in the process that is presently hindered by the combination of a rapid heat build-up in the substrate component and the mismatch between a relatively low thermal expansion coefficient of the ceramic coating and much higher thermal expansion coefficients of typical substrate materials.
A new, cryogenic nitrogen gas (-195C) cooling system has been developed which limits the thermal expansion and overheating problems, enables a non-stop, gun-on-target spraying, and eliminates the need for inter-pass cooling breaks experienced even with forced air and CO2 cooling. Fully automated, the operation of the AP LIN-Cooling System is based on real-time, thermal imaging of the entire substrate component and multi-zone surface cooling with novel, cryo-fluidic jetting nozzles. Thermal logs and images of all components processed are saved by the system for QA and auditing purposes.
This paper presents results of industrial tests of the system during the WC-CoCr coating of Boeing 737 landing gear including a 50% reduction in the effective spraying time, along with the corresponding reduction in the consumption of powder and process gases, and the additional savings due to the use of soft, flexible masking, not feasible with the traditional cooling methods. The effect of cooling on coating microstructure, adhesion, composition, properties of substrate material, and evolution of interfacial residual stresses will be presented and discussed.
|
|