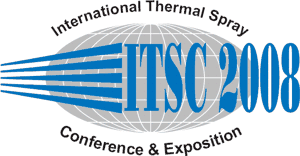 |
Abstract No.: |
|
Scheduled at:
|
Wednesday, June 04, 2008, Room 08 1:40 PM Diagnostics and Sensors 2 Modern process diagnostics offer a lot of possibilities for gaining data for both quality control and process knowledge. The recorded data is the base for process models and enhances the process knowledge
|
|
Title: |
Thermal spraying as a manufacturing technology for light metal MMC; experimental and numerical process analysis
|
|
Authors: |
Martin Silber* / Universität Stuttgart
Institut für Fertigungstechnologie keramischer Bauteile, IFKB / Institute for Manufacturing Technologies of Ceramic Components and Composites, Germany Esther Dongmo / Universität Stuttgart, Institute for Manufacturing Technologies of Ceramic Components and Composites, Germany Martin Wenzelburger/ Universität Stuttgart, Institute for Manufacturing Technologies of Ceramic Components and Composites, Germany Rainer Gadow/ Universität Stuttgart, Institute for Manufacturing Technologies of Ceramic Components and Composites, Germany
|
|
Abstract: |
For the manufacturing of metal matrix composites, a combined process of thermal spraying followed by forging in the semi-solid state can be applied. In previous work, it has been shown that thermal spraying leads to a globular microstructure that is suitable for semi-solid forming, and penetration of the spray material into the reinforcement phase leads to reduced matrix flow paths and thus reduced forming time and fiber disarrangement during the forming process. The main requirement is a low substrate and coating temperature during matrix deposition. By control of the process temperature, geometrical accuracy of the prepreg material and it?s handling between each process step can be significantly improved, leading to an economical method that is a superior alternative to the well established MMC processes like diffusion bonding or squeeze casting. Moreover, due to low process temperatures and process time during matrix application, chemical attack of carbon fiber reinforcements can be reduced. Process development for the manufacturing of continuous fiber reinforced prepregs was focused on the analysis and control of particle properties and substrate temperature. In order to improve the temperature control during arc wire spraying, numerical process analysis of the cooling system was applied. Particle in-flight analysis with the SprayWatch® system was used to obtain direct spray parameters as input data for the numerical models. The simulation results were verified by experimental infrared thermography of the substrate during coating. By the use of an optimized cooling system, dense coatings without cracks were achieved with different coating thickness, thereby tailoring the fiber volume content of the final MMC component.
|
|