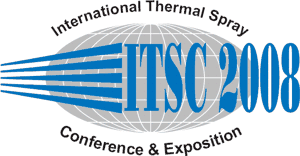 |
Abstract No.: |
|
Scheduled at:
|
Monday, June 02, 2008, Room 08 2:20 PM Plasma Spraying and Plasma Transferred Arc 1 New trends and modified plasma processes for the application of ceramic-based coatings
|
|
Title: |
VPS tungsten coatings sprayed by direct current (DC) and inductive coupled (IC) plasma
|
|
Authors: |
Heiko Gruner / MEDICOAT AG, CH Jan Moens* / Medicoat AG, Switzerland Philipp Gruner/ Medicoat AG, Switzerland
|
|
Abstract: |
Tungsten and its alloys are well suited for high temperature/high vacuum applications due to the high melting point (3410 °C) and low vapour pressure (1.3 x 10-7 Pa). Dense and oxide free W-coatings are needed for different applications such as armor for highly loaded plasma-interactive components of near future fusion reactors, free standing parts or for X-ray shielding in X-ray components.
Dense and oxide free tungsten are preferably produced by inductive coupled (IC) vacuum plasma spraying due to the high energy/enthalpy of the (IC) plasma jet and the prolonged dwell time of the axial injected powder particles. Today a coating density up to 98 % is a standard.
The design and properties of the DC-plasma torch have a strong influence on the characteristics of the plasma jet. Key factor for an economic spraying process is the particle/plasma interaction, responsible for the dwell time, temperature and velocity of the radial injected powder particles that form the coating. Using our VPS-system that combines IC- and DC-spraying we have been producing tungsten coatings with both technologies using different spraying conditions. In this paper we will present the relationship between the DC-plasma nozzle design and the microstructure of the tungsten coatings prior and after thermal treatment in order to improve the coating density and the spraying efficiency at the same time. These data are also compared with the microstructure of coatings produced by means of IC-plasma spraying.
|
|