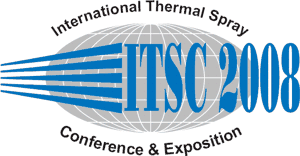 |
Abstract No.: |
|
Scheduled at:
|
Monday, June 02, 2008, Room 04 12:10 PM Wear Protection 1 Special processes for coatings against wear, improved surface roughness of as sprayed coatings, improved sliding behavior
|
|
Title: |
A microstructural study of cold sprayed Cu coatings on 2017 Al alloy
|
|
Authors: |
Kostoula Triantou* / NATIONAL TECHNICAL UNIVERSITY OF ATHENS
School of Naval Architecture and Marine Engineering
, GREECE C. Sarafoglou / National Technical University of Athens, Greece D. Pantelis/ National Technical University of Athens, Greece D. Christoulis/ Ecole des Mines de Paris - ParisTech, France V. Guipont/ Ecole des Mines de Paris - ParisTech, France M. Jeandin/ Ecole des Mines de Paris - ParisTech, France A. Zaroulias/ Pyrogenesis, Technological Park of Lavrio, Greece M. Vardavoulias/ Pyrogenesis, Technological Park of Lavrio, Greece
|
|
Abstract: |
Cold Gas Dynamic Spray (CGDS) or Cold Spray is an emerging and promising high rate material deposition process. The cold spray technique is based on the high velocity (300-1200 m/s) impinging of small solid particles on the substrate. In this process, the particles are accelerated by the supersonic gas jet at the heated gas temperature, which is usually lower than the melting point of the powder material. In this paper, copper coatings on 2017 Al alloy were obtained using Cold Spray. The surface roughness and the microhardness of the coatings were measured. The microstructure of the coatings was studied using optical microscopy as well as scanning electron microscopy. Ra parallel to the spray direction was almost equal to Ra perpendicular to the spray direction for all the coatings. It seemed that for the same powder flow and increasing pressure from 20 to 25 bar, the coating?s surface roughness tended to decrease. On the contrary, for the same pressure and increasing powder flow from 22 to 130 g/min, the coating?s surface roughness tended to increase. After etching of the coatings, particle ? particle interfaces and in some cases grain boundaries are revealed. Twins were observed in some of the coatings. Negligible porosity, absence of cracks and good adhesion of the coatings to the substrate are observed. Coatings have different thickness. It seemed that for the same powder flow and increasing pressure from 20 to 25 bar the thickness of the coating tended to increase. Also, it seemed that for the same pressure and increasing powder flow from 22 to 130 g/min, the thickness of the coating tended to increase. No differences were found in particle?s mean diameter and average particle?s deformability between the studied coatings. Coatings of higher thickness had lower average microhardness values at about 40- 50 HV0.3. It seemed that for the same powder flow and increasing pressure from 20 to 25 bar the average microhardness of the coating tended to decrease. Also, it seemed that for the same pressure and increasing powder flow from 22 to 130 g/min the average microhardness of the coating tended to decrease. HVOF Cu coating was studied for comparison with the cold sprayed coatings.
|
|