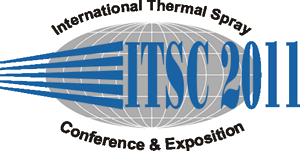 |
Abstract No.: |
|
Scheduled at:
|
Wednesday, September 28, 2011, Saal B2.1 12:40 PM Alternative Power Generation
|
|
Title: |
Cavitation erosion mechanism in Fe-Mn-Cr-Si-Ni arc thermally sprayed coatings
|
|
Authors: |
Anderson Pukasiewicz* / Universidade Tecnológica Federal do Paraná, Brazil André Capra / Institute of Technology for Development, Brazil Ramón Paredes/ Federal University of Paraná, Brazil Ana Sofia d'Oliveira/ Federal University of Paraná, Brazil
|
|
Abstract: |
Cavitation erosion is a common phenomenon that occurs in turbine blades and result in mass loss. Welding is the most common technique used to recover the geometrical profile of these cavited turbine blades, however it is known that tensile residual stress can develop. The development of manufacture process that could reduce or eliminate the residual stress level will contribute for a longer service life of this component. It is aimed in this study to evaluate cavitation erosion mechanism of Fe-Mn-Cr-Si-Ni arc thermally sprayed coating. Coatings were analyzed by optical and scanning eletronic microscopy, microhardness, cavitation tests (ASTMG32-92) and the analysis of eroded surface areas after ultrasonic cavitation tests with DRX and SEM. The results showed that lamellae morphology, oxide volume fraction and porosity were modified by chemical composition of the coatings, with reduction in area fraction oxide and microhardness with Ni addition. It was observed that Ni addition improve cavitation resistance by intersplats cohesion improvement. After ultrasonic cavitation tests, it was verified that mass loss occurred by interlamellae oxide removal and splats surface deformation in initial stages, followed by rupture and finally detachment of the lamellae. Splashing droplets promove a mass loss increase in some localized areas because their lower intersplats cohesion.
|
|