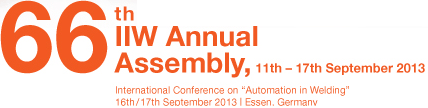 |
Abstract No.: |
|
Scheduled at:
|
Monday, September 16, 2013, Hall Europa 3:45 PM Session 2: Friction Stir Welding and Resistance Welding
|
|
Title: |
Robotic friction stir welding of primary structural elements of a medium-size aircraft
|
|
Authors: |
Jorge F. dos Santos* / Helmholtz Zentrum Geesthacht GmbH
Institute of Materials Science
Materials Mechanics, Solid-State Joining Processes, Germany Arne Roos / Helmholtz Zentrum Geesthacht, Germany Fernando Fernandez/ EMBRAER, Brazil Marcio Cruz/ EMBRAER, Brazil Andreza Viliotti/ EMBRAER, Brazil Marcos Miyazaki/ EMBRAER, Brazil
|
|
Abstract: |
Aircraft manufacturers are continuously searching for ways to reduce structural weight and improve production technology. Friction Stir Welding (FSW) belongs to the group of green manufacturing processes and has shown to be highly suitable for the joining of high strength aluminium alloys. The potential for the use of FSW in airframes is extremely large and the benefits of replacing mechanical fastening or NC machining significant. It has been shown that for airframe alloys cost and weight savings of at least 10% can be anticipated compared to mechanical fastening. One potential structural element is the joint of window frames to the fuselage. Conventionally this is a three dimensional riveted joint between a high strength rolled Al alloy (AA2024-T351) and a forged piece made of an AA7050 alloy. Within the scope of this project a welded solution has been proposed. Initially a process parameter window has been determined. Welds were produce to obtain samples for an extensive testing programme. This programme involved the determination of damage tolerance relevant mechanical properties such as fatigue and fatigue crack propagation. In the second phase of the project technology demonstrators were produced. This involved the manufacturing of clamping elements, robot programming and manufacturing the parts The friction stir joints revealed superior mechanical properties with values comparable to those of the base material. The welding speed proved to be twice as fast as the riveting feed rate. The complete structural element has been successfully welded by the tricept 805 robot, consisting of: two skin/window frame joints, 6 overlap skin/stringer rows and a butt joint between the two section. Based on these results, a 1:1 fuselage section has been produced and tested (barrel test) in large-scale testing facilities belonging to EMBRAER. The welded structured resisted 6,5 lives without detectable crack in the butt and lap joints.
|
|