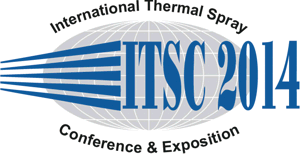 |
Abstract No.: |
|
Scheduled at:
|
Friday, May 23, 2014, Hall H1 10:00 AM Aviation Industry 3
|
|
Title: |
Modification of thermal sprayed coatings by sealing
|
|
Authors: |
Alsu Akhmetgareeva* / Technological Systems for Protective Coatings, Ltd., Russian Federation Lev Baldaev / Technological Systems for Protective Coatings, Ltd, Russian Federation Sergey Baldaev/ Technological Systems for Protective Coatings, Ltd, Russian Federation Ivan Mazilin/ Technological Systems for Protective Coatings, Ltd, Russian Federation Svetlana Muhametova/ Technological Systems for Protective Coatings, Ltd, Russian Federation
|
|
Abstract: |
Thermally sprayed coatings are porous. The porosity originates from several different factors: partially or totally unmolten particles, inadequate flow rate or fragmentation of molten particles at impact, shadowing effect due to lower than optimal spray angle, and entrapped gas. Also it depends from spraying method, equipment and other factors. Such structural defects are detrimental for the coating corrosion resistance and decrease mechanical properties and wear resistance. The development of high velocity spraying methods reduces the porosity, but penetration of corrosive environment to the substrate can be prevented only by using coating surface modification. Many researchers tried to improve resistance to corrosion and erosion of thermally sprayed coatings. Treatment was performed by impregnation with liquid metals, salts of phosphoric acid, laser treatment, a mixed deposition, heat treatment, hot isostatic pressing (HIP), sol-gel treatment, chemically vapor deposition (CVD coatings), etc. Depending on the environment conditions and type of thermal sprayed coating we have developed optimal sealing composition to improve the corrosion and abrasion resistance. The following types of conditions and coatings were chosen: high-temperature media of the gas turbines with APS ceramic coating and highly erosive media of oil drilling equipment with HVOF cermet coating. Sealed coatings were studied by means of cross-section optical microscopy, SEM, XRD, EDS. It was shown that sealing treatment allows to improve sulphuric and vanadium-induced high-temperature corrosion resistance (furnace cycling), general corrosion resistance (ASTM B117) and erosion resistance (ASTM G65).
|
|