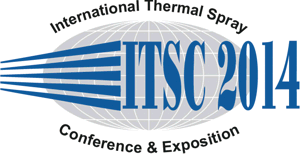 |
Abstract No.: |
|
Scheduled at:
|
Wednesday, May 21, 2014, Hall H1 & H2 3:54 PM "Young Professionals"
|
|
Title: |
Influence of the powder morphology and plasma spray process parameters on the Al2O3 based coating structure and properties
|
|
Authors: |
Ville Matikainen* / Tampere University of Technology, Finland Heli Koivuluoto/ Tampere University of Technology, Finland Jussi Larjo/ Oseir Ltd., Finland Petri Vuoristo/ Tampere University of Technology, Finland
|
|
Abstract: |
Plasma-sprayed alumina (Al2O3) is commonly used as a wear resistant coating material in demanding applications. Improved coating characteristics can be achieved by using agglomerated and sintered (A/S) Al2O3 powders with small additions of e.g. titania (TiO2) or chromia (Cr2O3), instead of blended fused and crushed (F/C) powders. However, the round particle morphology specific to the A/S powder manufacturing process accompanied by lower particle density and higher particle surface area change the injection and melting properties of the particles. It is, therefore, essential to take into account the size distribution and the density of the sprayed powder in the spray process. Changes in the plasma spray and powder injection parameters are necessary to optimise the coating structure, e.g. amount of partially melted particles. Spray diagnostics can be used to assist in this process optimisation. Now-a-days robust and simple camera systems are available to measure the spray stream characteristics and particle velocities. In this study, both the F/C and the A/S alumina based powders were sprayed by using a conventional plasma torch with a radial powder injection. The plasma spray process and powder injection parameters were optimised and the injection behaviour of the A/S powders was studied. Changes in the spray stream characteristics caused by the carrier gas flow rate and plasma spray parameters were measured with novel spray diagnostics equipment. The coating structures were studied with SEM and coating properties, e.g. hardness and wear resistance were evaluated.
|
|