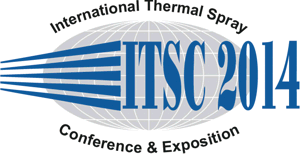 |
Abstract No.: |
|
Scheduled at:
|
Friday, May 23, 2014, Hall H1 3:00 PM Ceramic Coatings 2
|
|
Title: |
Investigation of crack propagation behavior of thermal barrier coatings fabricated by atmospheric plasma spraying in the process of uniaxial tension using acoustic emission technique
|
|
Authors: |
Liang Wang* / Shanghai Institute of Ceramics, Chinese Academy of Sciences, China Xinghua Zhong / Shanghai Institute of Ceramics, Chinese Academy of Sciences, China Yuexing Zhao/ Shanghai Institute of Ceramics, Chinese Academy of Sciences, China Huayu Zhao/ Shanghai Institute of Ceramics, Chinese Academy of Sciences, China Jiasheng Yang/ Shanghai Institute of Ceramics, Chinese Academy of Sciences, China Shunyan Tao/ Shanghai Institute of Ceramics, Chinese Academy of Sciences, China You Wang/ Harbin Institute of Technology, China Xiaoguang Sun/ Harbin Institute of Technology, China
|
|
Abstract: |
To characterize the adhesive strength of the plasma sprayed thermal barrier coatings (TBCs) via uniaxial tension is a common technique. In this paper, the crack initiation and propagation behavior in the atmospheric plasma sprayed (APS) TBCs in the process of uniaxial tension test has been investigated using the acoustic emission (AE) methods, X-ray diffraction (XRD), scanning electron microscope (SEM), and finite element method (FEM). The experimental results indicate that the position of the crack initiation is usually located in the inner of the ceramic layer, and the crack tend to propagate along the tension direction and some key cracks reach to the metallic layer/ceramic layer interface, then the cracks propagate along the interface. When some big enough pores was formed at the interface and a series assembled splats separated from the coating, the coating totally failure. The AE signal can be divided into three typical stages which corresponds to the three stages of the stress -stain curve of the tension. The detailed analysis of the AE signal has been performed. The dynamic propagation patterns of the key cracks in the ceramic layer during the tension process has been simulated using FEM based on the computational micro-mechanical (CMM) method which considered the real microstructual image of the TBC. The finite element simulation results has further prove our conclusions drawn from the experimental results.
|
|