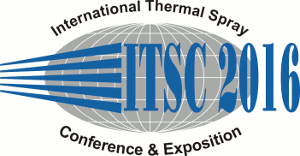 |
Abstract No.: |
|
Scheduled at:
|
Wednesday, May 11, 2016, Room 3H + 3I + 3J 3:40 PM Arc Spraying & Laser Spraying
|
|
Title: |
Closed-loop control tools for automated laser cladding processes
|
|
Authors: |
Andreas Wank* / GTV Verschleißschutz GmbH, Germany Frank Beck / GTV Verschleiss-Schutz GmbH, Germany Jochen Zierhut/ Zierhut Messtechnik GmbH, Germany Klaus Kloiber/ Zierhut Messtechnik GmbH, Germany
|
|
Abstract: |
As costs of laser sources have decreased strongly laser cladding and laser additive manufacturing have become fast-growing technologies due to the inherent advantages like high precision of material deposition, flexibility concerning achievable coating thickness and deposition rates, metallurgical bonding to substrate materials, low porosity and fine microstructure deposits, relatively low heat transfer to substrates and aptitude for process automation. However, there is a multitude of applications that require closed-loop control tools in order to permit complete process automation. For example change of component temperature during the cladding process, e.g. for cladding of small wall thickness components, results in need of tools to adjust laser power. And in order to fill cavities like grooves precisely despite distortion and thermal expansion of components to be clad edge recognition systems for adjustment of laser head movement are needed. GTV Verschleiss-Schutz GmbH and Zierhut Messtechnik GmbH jointly developed LPowC (Laser Power Control) and LPosC (Laser Positioning Control) systems based on digital image analyses to address these needs. Both tools are based on intelligent cameras that evaluate recordings from the cladding zone through the optical path of the laser optics. While LPowC controls local emission by the laser cladding process, LPosC detects distances between edges on component surfaces and laser spot as a base for positioning correction. Exemplary cladding of thin wall tubes with different iron, nickel and cobalt based alloys with automatic adjustment of laser power and the effect on local microstructure of the deposits are presented as well as evaluation of filling of grooves on shafts that undergo strong cooling during the cladding process.
|
|