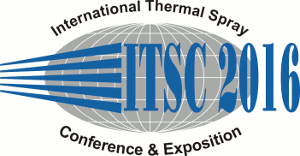 |
Abstract No.: |
|
Scheduled at:
|
Thursday, May 12, 2016, Room 3C + 3D 10:20 AM New Processes II
|
|
Title: |
Performance and economic characteristics of multi-chamber detonation sprayer using in the thermal spray technology
|
|
Authors: |
Jeff Jia / Beijing United Coatings Technologies Co., China Yu. Tyurin / E.O. Paton Electric Welding Institute, NASU, Ukraine M. Kovaleva/ Belgorod State National Research University, Joint Research Center, Russia N. Vasilik/ N.N. Semenov Institute of Chemical Physics, RAS, Russia V. Kolisnichenko/ E.O. Paton Electric Welding Institute, NASU, Ukraine M. Prozorova/ Belgorod State National Research University, Joint Research Center, Russia M. Arseenko*/ Belgorod State National Research University, Joint Research Center, Russia V. Sirota/ Belgorod State National Research University, Center for Constructional Ceramics and the Engineering Prototyping, Russia
|
|
Abstract: |
Multi-chamber detonation sprayer (MCDS) consists of the specialized chambers for mixing of the components of the combustible mixture, circular prechamber for the initiation of the detonation regime of combustion, cylindrical and disk combustion chambers and a barrel. Synchronization and summation of energy of products of detonation combustion from the cylindrical and disc chambers is realized in MCDS. As a result, the pulse jet of combustion products at speeds up to 3000 m/s is formed in the barrel. MCDS completed with a feeder and a device for synchronization of the input portions of the powder with a pulse of combustion products. The barrel is replaceable and can have a diameter from 12 to 30 mm, and a length 200 mm, 300 mm and 500 mm, respectively for metal, cermet and ceramic powders. The exact dosing and feed of powder into the barrel provide high deposition efficiency before the initiation of detonation. The deposition efficiency is 80-90% and 70-80%, respectively for cermet and ceramic powders. Flow rate of fuel mixture components are 0.6-1.2 m3/h of propane and 3.0-6.0 m/h of oxygen with productivity up to 4 kg/h (metal powders), up to 2 kg/h (cermet powders) and up to 1 kg/h (ceramic powders).
|
|