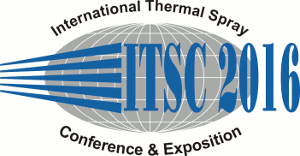 |
Abstract No.: |
|
Scheduled at:
|
Tuesday, May 10, 2016, Auditorium 3:45 PM Young Professionals Session
|
|
Title: |
Warm spraying of high strength Ni-Al-Bronze for cavitation protection
|
|
Authors: |
Sebastian Krebs* / Helmut-Schmidt University, University of the Federal Armed Forces Hamburg, Dep. of Materials Engineering, Germany Simon Frede / Helmut-Schmidt University, University of the Federal Armed Forces, Germany Hiroshi Araki/ National Institute for Materials Science, Japan Hiroshi Katanoda/ Kagoshima University, Japan Frank Gaertner/ Helmut-Schmidt University, University of the Federal Armed Forces, Germany Seiji Kuroda/ National Institute for Materials Science, Japan Thomas Klassen/ Helmut-Schmidt University, University of the Federal Armed Forces, Germany
|
|
Abstract: |
Ni-Al-bronzes show exceptional good performance against corrosion, erosion and cavitation-erosion and are typically in use as cast materials for ship propellers, fluid systems or in applications with alternating stresses. Thereby, the high cavitation resistance of Ni-Al bronzes is attributed to a combination of high fatigue strength and high resistance against plastic deformation. Since processing massive parts of Ni-Al bronze is costly, applying coatings onto exposed areas could be a favorable solution for increased life times of parts in the ship-building industry. First experiments with cold gas sprayed bronze coatings demonstrated good coating performance, particularly a high cavitation resistance. Nevertheless, the full potential of possible solutions could not be explored. Prone to nozzle clogging, cold spraying of Ni-Al bronze was limited to a process gas temperature of maximum 700°C. Warm spraying could offer possible solutions to overcome such process temperature limitation. In warm spraying, coatings are formed at similarly high particle velocities but higher process temperatures as compared to cold spraying. By well tuning the impact temperatures, oxidation also could be limited. This study systematically evaluates the formation of warm sprayed Ni-Al-Bronze coatings under variation of the combustion pressure and the nitrogen flow-rates. One-dimensional analysis of gas/particle flow was used to determine particle impact velocity and temperature under the different spray parameter sets. Coating microstructures and cavitation properties are discussed under viewpoints of the calculated particle impact conditions. In addition, substrate pre-heating was used to improve coating properties, particularly coating adhesion. Under optimized warm spray conditions, the warm sprayed coatings showed low porosities, high mechanical strengths and a cavitation resistance, that is almost comparable to that of respective bulk material. Thus, warm spraying could offer solutions for improving service life of marine equipment.
|
|