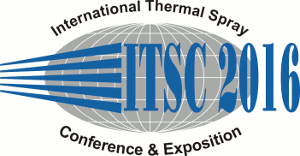 |
Abstract No.: |
|
Scheduled at:
|
Thursday, May 12, 2016, Room 3G 2:00 PM Plasma Spraying
|
|
Title: |
Comparison of ZrB2-MoSi2 composite coatings fabricated by atmospheric and vacuum plasma spray processes
|
|
Authors: |
Kai Li / Shanghai Institute of Ceramics, Chinese Academy of Sciences, Shanghai Yaran Niu* / Shanghai Institute of Ceramics, Chinese Academy of Sciences, China Wang Zhong/ Shanghai Institute of Ceramics, Chinese Academy of Sciences, China Li Hong/ Shanghai University, China Zheng Xuebin/ Shanghai Institute of Ceramics, Chinese Academy of Sciences, China Sun Jinliang/ Shanghai University, China Ding Chuanxian/ Shanghai Institute of Ceramics, Chinese Academy of Sciences, China
|
|
Abstract: |
Ultra-high temperature ceramics (UHTCs) are potential thermal protective materials due to their extremely high melting point. Zirconium diboride (ZrB2) is typical among UHTCs owing to its unique combination of properties. However, the poor oxidation resistance of ZrB2 limits it for extreme environment applications. MoSi2is generally chosen as additive to improve the oxidation resistance of ZrB2-based composites. In this work, ZrB2-20vol.%MoSi2 composite coatings were fabricated by atmospheric plasma spray (APS) and vacuum plasma spray (VPS) technologies, respectively. Phase composition and microstructure of the composite coatings were characterized. Physical properties, including porosity, oxygen contentandmicrohardness of the coatings were examined.Their oxidation behaviors and microstructure changes at 1773 K were comparatively investigated.The results showed that the VPS-ZrB2/MoSi2 coating was composed of hexagonal ZrB2, tetragonal and hexagonal MoSi2. While amount of ZrO2 was formed for the APS-ZrB2/MoSi2 coating.Oxide content and porosity in the VPS-ZrB2/MoSi2 coating were apparently lower than those of the APS-ZrB2/MoSi2 coating. The weight gains of the APS-ZrB2/MoSi2 coating were higher than that of the VPS-ZrB2/MoSi2 coating after oxidation at 1500oC for 0-6h.The VPS-ZrB2/MoSi2 coating presented more compact microstructure and better oxidation resistance than the APS-ZrB2/MoSi2coating, having potential application as high-temperature protecting coating.
|
|