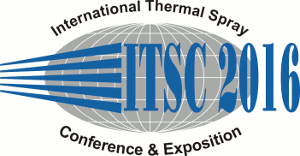 |
Abstract No.: |
|
Scheduled at:
|
Thursday, May 12, 2016, Yellow River Hall 11:40 AM Power Generation III
|
|
Title: |
Vacuum plasma coating systems (LPCS, VPS, Hybrid) for plasma spraying of gas turbine components for applications throughout Asia
|
|
Authors: |
Robert Gansert* / Advanced Materials & Technology Services, Inc., USA Ralph Herber/ AMT AG, Switzerland Danilo Lazzeri/ AMT AG, Switzerland Silvano Keller/ AMT AG, Switzerland
|
|
Abstract: |
AMT AG (Dottingen, Switzerland) has designed Low Pressure Coating Systems (LPCS), Vacuum Plasma Systems (VPS) and Hybrid systems for plasma spraying of gas turbine engine components for applications throughout Asia. An increase in air transportation and energy needs throughout Asia and emerging markets has necessitated the increased use of low pressure plasma spray and vacuum coatings for turbine engine applications around the world. AMT AG has designed plasma spray for the application of nickel-based (MCrAl, MCrAlY) coatings for such parts. Coatings produced using the LPCS and VPS provide improved oxidation protection to gas turbine engine components utilizing thermal barrier coating systems.
The LPCS consists of a main vacuum process chamber, with load-locks for part loading and unloading, gun drives, work-piece manipulators (stings), vacuum system, and a high power plasma spray system. In comparison, vacuum plasma typically consists of a main process chamber with a robot located inside the chamber without use of stings. Hybrid systems are also built which consist of attributes of these former two systems. Process and configuration differences between these systems will be examined.
Nickel-based (e.g., nickel-chromium-aluminum-yttrium) coatings will be produced with LPCS and VPS. The benefits of each system will be discussed and compared to other traditional air plasma spray coatings. Experiments will be performed to examine coating properties as a function of plasma spray parameters. Microstructure and mechanical property evaluations will be conducted for the LPCS and VPS produced coatings. Microstructural analysis will be conducted evaluating coating buildup, oxides and porosity using optical microscopy, and mechanical property analysis evaluating microhardness, macrohardness and tensile adhesion strength.
|
|