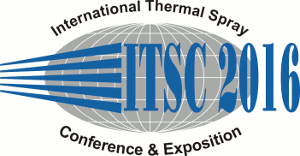 |
Abstract No.: |
|
Scheduled at:
|
Wednesday, May 11, 2016, Room 3H + 3I + 3J 1:40 PM Power Generation - Fuel Cell II
|
|
Title: |
Protective coatings for SOFCs deposited using different plasma spray techniques
|
|
Authors: |
Francesco Bozza* / Turbocoating S.p.a., Italy Nelso Antolotti / Turbocoating S.p.a., Italy Martin Thoma/ MT Consulting, Germany Enea Ghidini/ Turbocoating S.p.a., Italy Luca Tagliaferri/ Turbocoating S.p.a., Italy
|
|
Abstract: |
Nowadays stainless steel is the most employed material for interconnectors in solid oxide fuel cells (SOFC). The corrosion resistance is achieved by adding 20-25 wt-% chromium to the steel. At operating conditions, these steels form a double-layered structure (chromium-oxide and chromium-manganese-oxide) at the surface, which prevents further oxidation. However, chromium is prone to evaporate at the operating temperature. Chromium poisoning is a widely recognized degradation mechanism in SOFCs. The gaseous Cr-rich compounds, formed during the working life, reach the cathode material leading to an overall loss of efficiency of the SOFC and to a premature failure of the stack. Manganese-cobalt-oxide spinel (MCO) and manganese-cobalt-oxide doped with iron (MCF) were found to be potential candidates to prevent Cr evaporation. Those spinels are applied to form a thin and dense coating on the surface of the steel interconnector, to act as a barrier against Cr diffusion, without decreasing the electrical conductivity of the interconnector. The aim of the present work, carried out as a part of the EU funded project SCORED 2:0, was to investigate in detail the behavior of MCO and MCF coatings applied by atmospheric plasma spray (APS) on different stainless steels (K41, Sanergy HT and Crofer 22H). Traditional plasma spray with powders as feedstock material and innovative suspension plasma spray (SPS) were employed. SPS allowed to obtain a thinner and denser coating, with superior properties. Exposure tests and area specific resistance measurements were performed in order to evaluate the ohmic resistance and the Cr-evaporation rate of the deposited layers. The evolution of the coating microstructure was evaluated by means of SEM and XRD analysis. After laboratory-scale tests, MCO and MCF coatings were deposited on real parts and long term tests were performed in order to evaluate the behavior of an assembled stack.
|
|