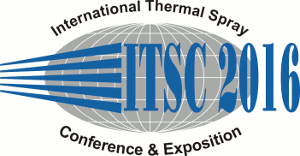 |
Abstract No.: |
|
Scheduled at:
|
Tuesday, May 10, 2016, Yellow River Hall 2:00 PM Wind & Offshore
|
|
Title: |
Long-term marine exposure test of HVOF sprayed 316L stainless steel and hastelloy C-276 coatings
|
|
Authors: |
Seiji Kuroda* / National Institute for Materials Science, Japan Jin Kawakita/ National Institute for Materials Science, Japan Takeshi Fukushima/ National Institute for Materials Science, Japan Masayuki Komatsu/ National Institute for Materials Science, Japan Hiroshi Araki/ National Institute for Materials Science, Japan
|
|
Abstract: |
Even though HVOF sprayed coatings of various metals and alloys can be highly dense, whether they can perform as a corrosion barrier in a severe corrosive environment such as sea water is a big question. After a series of laboratory corrosion tests of HVOF sprayed 316L stainless and Hastelloy C-276 coatings sprayed by a commercial apparatus, i.e., JP5000 (TAFA) and by a modified version with a gas-shroud attachment, coatings with high density and minimum degree of oxidation have been selected for tests in a marine exposure test site in Chiba prefecture in Japan since 2000. The initial test specimens were A4 size plates, 400 micron thick coatings were fabricated on a 5mm thick carbon steel substrate. All side edges were sealed with heavy duty tar-epoxy resin to allow only the flat surface to be tested. Later, cylindrical specimens without resin sealing were prepared with promising coating specifications. These specimens were set in a test rig at three levels, i.e., the splash, tidal and immersed zones.
All of these samples were taken out from the test sites in 2015 and have been inspected. The main results are summarized as the following.
1) 316L stainless coatings could not provide sufficient corrosion protection in all the zones. 2) For Hastelloy coatings, gas-shroud attachment showed a significant improvement in coatings corrosion resistance. 3) Generally, life was longer in the splash zone as compared to the tidal and immersed zones. 4) Surface polishing provided significant merit in prolonging the life. 5) Coatings heat treated at 1,000 degree C for 1 hour did not show any sign of failure for 15 years in all the testing zones.
|
|