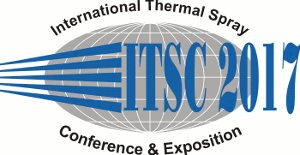 |
Abstract No.: |
|
Scheduled at:
|
Thursday, June 08, 2017, Hall 27 11:00 AM HVAF Spraying
|
|
Title: |
Effect of nozzle geometry on the microstructure and properties of HVAF sprayed hardmetal coatings
|
|
Authors: |
Ville Matikainen* / Tampere University of Technology, Finland Heli Koivuluoto/ Tampere University of Technology, Finland Petri Vuoristo/ Tampere University of Technology, Finland
|
|
Abstract: |
Thermally sprayed hardmetal coatings are the industrial standard solution for numerous demanding applications. Often the performance of thermally sprayed coatings is improved by using finer particle sizes due to decreased coating surface roughness and defect sizes. In the aim of utilizing finer particle and primary carbide sizes in thermal spraying of hardmetal coatings, several approaches have been studied to control the spray temperature. The most viable solution is to use the modern high velocity air-fuel (HVAF) spray process, which has already proven to produce high quality coatings with dense structures. In HVAF spray process, the particle heating and acceleration can be efficiently controlled by changing the nozzle geometry. In this study, fine WC-10Co4Cr powder (-25+5 µm) was sprayed with three nozzle geometries to investigate their effect on the particle temperature, velocity and coating microstructure. The study demonstrates that the particle heating and W2C formation could be efficiently controlled by changing the nozzle geometry from cylindrical to convergent-divergent. Moreover, the average particle velocity was increased from 780 to over 900 m/s. This increase in particle velocity significantly improved the coating structure and density while deposition efficiency decreased slightly. Further evaluation was carried out to resolve the effect of particle in-flight parameters on cavitation erosion resistance, which was significantly improved with the increasing average particle velocity.
|
|