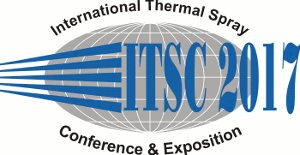 |
Abstract No.: |
|
Scheduled at:
|
Thursday, June 08, 2017, Hall 12 10:00 AM Automotive Industry
|
|
Title: |
Thermal spray coatings as friction surfaces of lightweight brake rotors
|
|
Authors: |
Septimiu Popa* / University of Stuttgart, Germany Rainer Gadow / Insitute for Manufacturing Technologies of Ceramic Components and Composites, University of Stuttgart, Germany Andreas Killinger/ Insitute for Manufacturing Technologies of Ceramic Components and Composites, University of Stuttgart, Germany
|
|
Abstract: |
Thermal spraying is an industrially widespread coating technology for manufacturing performant protective and functional coatings for a variety of challenging applications. In the automotive industry, thermal spray coatings are successfully used in series production: as thermal shock protection of lambda sensors, wear protective coatings on power chain components and as cylinder liner coatings, where the tribological properties are improved or even tailored and the crankcase weight is significantly reduced. In the present work the lightweight design potential is used as an engineering concept, where oxide-ceramic and cermet coatings are applied on light metal alloy brake rotors by atmospheric plasma spraying and High Velocity Oxy-Fuel spraying respectivley. Thereby, the layer composite component obtains on the one hand a wear and corrosion resistant surface with optimum braking characteristics where on the other hand the substrate material enables significant weight savings compared to the reference steel rotor, subsequently improving the handling characteristics of the car due to lower rotating and unsprung masses. The paper describes the development of the coated lightweight brake rotors focusing on the manufacturing process and coating properties. The studies also include brake dynamometer test with subsequent evaluation which show that the coated rotors posses improved breaking properties in comperason to the reference rotor. The brake rotors were successfully used in a Formula Student race car in international competitions; therefore certain aims were targeted during development, such as a temperature-independent constant friction coefficient and lower peak temperatures in order to meet the special competition specifications and challenges.
|
|