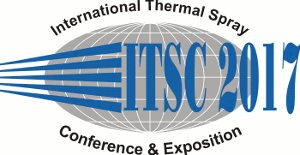 |
Abstract No.: |
|
Scheduled at:
|
Thursday, June 08, 2017, Hall 28 4:40 PM Cold Gas Spraying II
|
|
Title: |
An experimental approach to gain insight into cold gas spraying of ceramics
|
|
Authors: |
Henning Gutzmann* / Helmut-Schmidt-University of the Federal Armed Forces, Germany Ivan Irkhin / Helmut Schmidt University, Institute of Materials Technology, Germany Frank Gärtner/ Helmut Schmidt University, Institute of Materials Technology, Germany Thomas Klassen/ Helmut Schmidt University, Institute of Materials Technology, Germany
|
|
Abstract: |
Cold gas spraying of ductile metallic materials is very well established today. Manifold applications exist and numerous experiments and simulations led to a basically well investigated and understood process. However, for cold spraying of ceramics, only very little generally accepted knowledge exists up to date. Since the technique can avoid phase transformations and process ceramic material by preserving the crystallographic structure of the powder feedstock, it has a high application potential to develop functional coatings. In this study, an experimental approach to investigate basic dependencies on impact and bonding of agglomerated ceramic particles in cold spraying is presented. Single impact morphologies of ceramic particles obtained from wipe tests are correlated with data obtained from powder compression experiments with a modified nanoindenter. Different feedstock powders of agglomerated TiO2-nanoparticles were used and also partially heat treated. The single particle impacts were characterized by SEM. The powder shapes and sizes prior and after the compression tests were analyzed by confocal microscopy. The single impact events reveal that deformation and bonding of ceramic particles to metal substrates depend on substrate material, substrate temperature, spray conditions and powder properties. In particular, the powder characteristics appear as most influential for deformation and bonding in cold spraying of ceramics. To which degree particles fracture or contribute to layer formation highly depends on their individual deformation behavior.
|
|